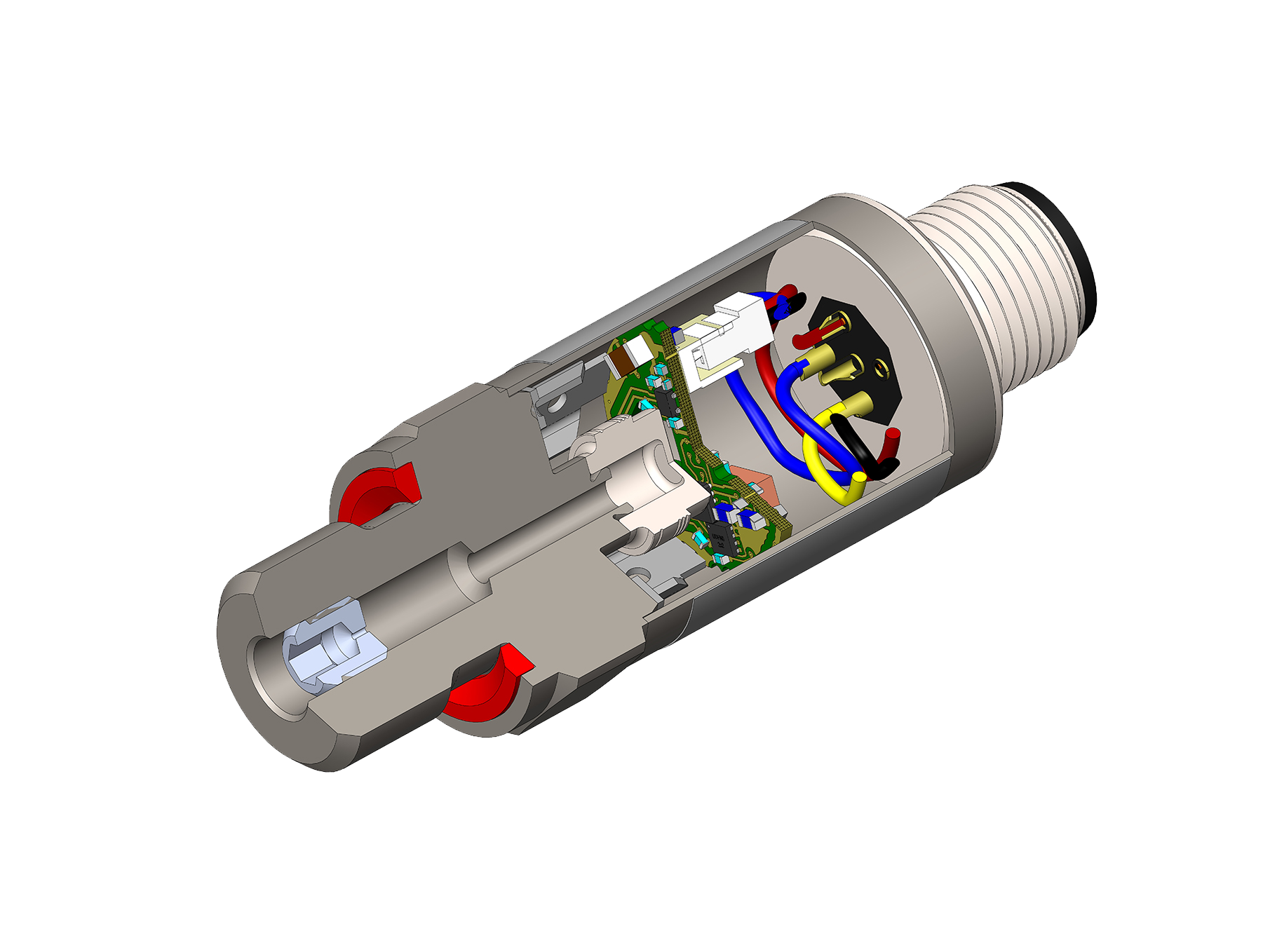
In pressure measurement technology, a distinction is made between absolute pressure, relative pressure and differential pressure. Absolute pressure always refers to the absolute vacuum as the zero point. Relative pressure measurement is the measurement of the differential pressure between a medium and the ambient or atmospheric pressure (approx. 1 bar).
The relative pressure is the difference between an absolute pressure and the atmospheric pressure.
Measuring principle of the relative pressure sensor.
The absolute pressure is the pressure relative to zero pressure in an absolute vacuum.
Measuring principle of the absolute pressure sensor
The measuring range is the pressure range between the minimum pressure (at which the output signal outputs 0 %) and the maximum pressure (at which the output signal outputs 100 %).
The difference between the minimum and maximum values is referred to as the span and serves as a reference for almost all accuracy specifications in pressure measurement technology. As a rule, the measuring range of pressure transmitters is standardized to a specific pressure measuring unit, e. g. bar, mbar or psi. In addition to the pure signal range, overpressure and burst pressure limits must also be taken into account. These are important in applications where pressure peaks – even very brief ones – can occur well above the measuring range.
Example
In practice, it has been shown that the definition of the required accuracy class or the permissible measurement uncertainty of the pressure gauge is a great challenge. On the one hand, the accuracy class includes various aspects or parameters of the measurement uncertainty, which does not have the same significance in most applications. On the other hand, it is also often difficult to determine how accurate the measurement actually needs to be on the application side. Higher accuracy almost always entails a massive impact on product cost. Therefore, it is important to weigh well what is mandatory when selecting the accuracy class.
For the output signal, a distinction is made between three main categories: Unamplified sensor signal, analog (standard) signals and digital signals. The output of the unamplified sensor signal is very rarely desired for pressure gauges; this is in contrast to temperature gauges, which very often provide the signal of the PT100/PT1000 resistor directly without additional electronics. If the unamplified sensor signal is now output, the pressure measuring instrument is not a transmitter or measuring transducer in the narrower sense. Rather, it is then referred to as a measuring cell with a housing. These are often also called transducers.
Analog signals are still the most widely used in pressure measurement technology in industry today, above all the current signal 4 ... 20 mA. The advantage of analog signals is still the significantly lower costs for pressure transmitters and often also for the downstream evaluation electronics.
However, the costs of digital transmitters and evaluation units have dropped significantly in recent years. In addition, the spread of sensor bus systems such as IO-Link or CANopen in pressure measurement is increasing rapidly. The main advantages of digital signals are the higher safety against errors, diagnostic and parameterization possibilities as well as the combination of several measurement parameters in one device, for example pressure and temperature. Electronic pressure switches are also counted among the pressure transmitters with digital signals. All information on electronic pressure switches can be found in another article
The pressure sensor is the core element of the pressure gauge. In pressure transmitters, this pressure sensor is usually an element where a change in pressure leads to a deformation of the diaphragm. This in turn leads to a change in electrical resistance on specially applied resistive elements. The most commonly used sensor technologies are thin-film-on-steel, thick-film-on-ceramic and piezoresistive sensors.
In thin-film-on-steel sensors, resistors are sputtered onto a stainless s teel diaphragm.The main advantage of these pressure sensors is their excellent long-term stability and high robustness against pressure peaks and temperature influences, as well as pressure measurement over large pressure ranges from about 200 mbar to over 3,000 bar.
Thick-film-on-ceramic sensors are based on a ceramic base body on which the resistance bridges are applied and then burned in. The ceramic membrane is considered to be extremely robust against almost all corrosive liquids and gases and is preferably used when aggressive chemicals have to be measured. The measuring ranges start at about 100 mbar and go up to about 400 bar.
In piezoresistive pressure sensors, the resistance of silicon semiconductor elements changes with pressure. These semiconductor elements are isolated from the measured medium by an oil filling and a thin separating diaphragm. Due to the high sensitivity and the low hysteresis of the silicon element, piezoresistive sensors are particularly suitable for low pressures in the mbar range and when higher accuracy is required.
The pressure port connects the pressure gauge to the process where the pressure is to be measured. The pressure sensing element inside the transmitter must be tightly connected to the pressure port – be it welded or with elastomer seals. There are countless different pressure connections on the market, whose geometry and dimensions are specified in standards (e. g. the pressure gauge connection in DIN EN 837-1). In addition to industry-specific preferences, the decisive factor in the choice of connections is above all the type of seal: metallic sealing or with elastomer seals.
Another important aspect about the pressure connection is the choice of the material as this part of the transmitter is in direct contact with the mesured media. Corrosive media requires special steel alloys or titanium.
Most pressure connections are designed so that the pressure transducer is connected to the measured medium with a pressure channel bore. However, if pressure or level is to be measured on highly viscous, pasty or crystallizing liquids, flush process connections are used.
Elastomer seals – also known as O-rings or profile seals – use cylindrical mounting threads. In a groove, the elastomer seal is compressed during assembly so that a sealing effect is created. The elastomer material must be selected so that it is compatible with the measured media and seals over the entire temperature range.
The metallic seals are either conical threads or sealing cones. They are each mechanically deformed by the counterpart in such a way that a sealing effect is created. For pressures above 1,000 bar, metallic sealing solutions are usually chosen. In addition, there are also copper and steel rings that seal similarly to elastomer seals.
There is less variety in the electrical connection because each industry segment uses only a few connector types. In general, it can be said that cable versions directly on the pressure transmitter are used less frequently because the cabling is more complex than for versions with connectors.
Main criteria for the selection of the suitable connection are the tightness against liquids and dust, the vibration resistance as well as the costs of measuring device and cabling including commissioning.
A special requirement for pressure transmitters can be the correct pressure equalization from the transmitter interior and the environment: In practice, many electrical connections can cause unexpected problems when measuring pressure.
Electrical connection with cable version.
Electrical connection with cable version.
Electrical connection with connector Deutsch DT04.
Electrical connection with connector Deutsch DT04.
Would you like to learn more about the terminology for pressure measurement instruments? Like the specifications «Non-linearity», «Hysteresis», «Best straight line»? Or «Total error band», «Switching differential» or «EMC protection»? These therms and many more are explained here:
Trafag is a leading global supplier of high-quality sensors and monitoring instruments for measurement of pressure, temperature and gas density. In addition to a wide range of standardised, configurable products, Trafag also develops tailored solutions for OEM customers.
Trafag, a Swiss-based company founded in 1942, is supported by a broad sales and service network in over 40 countries across the world. This allows Trafag to offer customers personalised and competent advice and ensures the best possible service. High-performance development and production departments not only guarantee the fast and reliable delivery of our high-quality and high-precision products, but also ensure that customisations can be implemented in a short time.